
1/ El micrómetro: Es un instrumento de medición cuyo funcionamiento está basado en el tornillo micrométrico que sirve para medir con alta precisión del orden de centésimas en milímetros (0,01 mm) y de milésimas de milímetros (0,001 mm) (micra)las dimensiones de un objeto.
(del griego micros, pequeño, y metron, medición), también llamado Tornillo de Palmer, es un instrumento de medición cuyo funcionamiento está basado en el tornillo micrométrico que sirve para medir las dimensiones de un objeto con alta precisión, del orden de centésimas de milímetros (0,01 mm) y de milésimas de milímetros (0,001 mm) (micra).
Para ello cuenta con dos puntas que se aproximan entre sí mediante un tornillo de rosca fina, el cual tiene grabado en su contorno una escala. La escala puede incluir un nonio. La máxima longitud de medida del micrómetro de exteriores normalmente es de 25 mm aunque existen también los de 0 a 30, por lo que es necesario disponer de un micrómetro para cada campo de medidas que se quieran tomar (0-25 mm), (25-50 mm), (50-75 mm), etc.
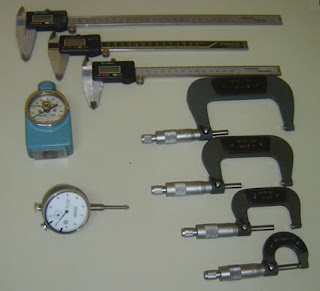
Frecuentemente el micrómetro también incluye una manera de limitar la torsión máxima del tornillo, dado que la rosca muy fina hace difícil notar fuerzas capaces de causar deterioro de la precisión del instrumento.
El micrómetro es también conocido como:
• micrón (plural: micrones), abreviado µ.
• micra (plural: micras; plural latino: micra), abreviado µ.
• En fabricación mecánica el micrón es la unidad de longitud más pequeña en la que se acotan las tolerancias de las cotas de las piezas que son rectificadas. la micra es una unidad de longitud muy importante.
Equivalencias
Un micrómetro equivale a una milésima de milímetro:
1 µm = 0,001 mm = 1 × 10-3 mm
1 mm = 1000 µm
Un micrómetro equivale a una millonésima de metro:
1 µm = 0,000 001 m = 1 × 10-6 m
1 m = 1 000 000 µm
Un micrómetro equivale a mil nanómetros:
1 µm = 1000 nm
1 nm = 0,001 µm
1 heit = 0,01 µm
Aplicación
El micrómetro es utilizado en diferentes ramas de la tecnología para realizar mediciones de precisión, pero es en la rama de la mecánica donde es utilizado con más frecuencia para la medición de piezas de gran precisión. Existen micrómetros de diferentes tipos según sea la medición que realice.
Lecturas Existen en el mercado micrómetros (palmer) de tres tipos, los de lectura grabada directa analógica, los de lectura con reloj analógico y los de lectura digital.
Despiece
El micrómetro (palmer) está por lo general fabricado en material de acero cromado en mate y esmaltado, el cual le da una calidad especial, también son fabricados en plástico y otros materiales. En las últimas generaciones de calibres interviene el plástico, sobre todo en los de reloj
instrumentos de medicion

Micrómetro o pálmer: es un instrumento que consta, de un montante o cuerpo en forma de U o herradura, presentando en uno de sus extremos una pieza cilíndrica roscada interiormente, siendo el paso de esta rosca de ½ mm o de 1mm. Esta pieza presenta además en su superficie externa una graduación longitudinal sobre una de sus generatrices de ½ en ½ milímetro. Dentro de esta pieza enrosca un tornillo, que al girar una vuelta completa, introduce uno de sus extremos dentro del espacio vacío de la herradura, avanzando por vuelta ½ mm o 1mm de acuerdo al paso que posee. Solidario al tornillo por el otro extremo se encuentra un tambor que por cada giro cubre a la pieza cilíndrica graduada una longitud igual al paso. El extremo del tambor indica en su avance la longitud que se introduce el tornillo dentro de la herradura. Esta última tiene en su extremo opuesto un tope fijo, regulable, que cuando hace contacto con la punta del tornillo indica longitud cero. El tambor tiene 50 o 100 divisiones según su paso sea de ½ mm o de 1 mm respectivamente sobre su perímetro circunferencial en el extremo que avanza sobre el cilindro graduado. Por tal motivo, cada división corresponderá a 0,01mm de avance o retroceso, lo que da la apreciación del instrumento.
Tipos especiales Existen diversas formas de micrómetros en el mercado, según sea la utilización que se le tenga que dar, las longitudes y formas de los topes son diferentes, en la siguiente lista están los más habituales:
• Con contactos planos, (DIN 863/1) medición de exteriores.
• Con contactos en cuchilla, (DIN 863/3) medición de exteriores,.como pueden ser las acanaladuras o ranuras estrechas.
• Con contactos con tope en forma de V y Vástago plano, (DIN 863/3) medición de exteriores, de herramientas de corte de 3 y 3 labios.
• Con contactos finos, (DIN 863/3) medición de exteriores de ranuras entalladas.
• Con contactos cónicos, (DIN 863/3) medición de exteriores de árboles con chavetas, ranuras y reducciones.
• Con contactos hemisféricos (Norma taller) medición de exteriores de superficies curvas, espesor de paredes de tubo, anillos, cojinetes.
• Con contactos de platillos, (DIN 863/3) medición de exteriores de engranajes.
• Con contactos intercambiables, (DIN 863/3) medición de exteriores de roscas.
Comentarios
Cuando decidamos adquirir un micrómetro tenemos que tener en cuenta la utilización que le daremos, el precio depende mucho de la calidad y precisión del mismo.
Denominación de la RAE de Micrómetro
2/ gramil: Un gramil es la herramienta usada en carpintería (ebanistería) o metalistería para marcar líneas paralelas de corte en referencia a una orilla o superficie, además de otras operaciones.
Consiste de una barra, un cabezal y un implemento de trazado que puede ser una tachuela, una cuchilla, un bolígrafo o una rueda. El cabezal se desliza a lo largo de la barra y puede fijarse en algún tramo mediante distintos instrumentos, ya sea un tornillo de retención, una leva de control o una cuña.
Gramil Es un instrumento de medición y trazado que se utiliza en los laboratorios de metrología y control de calidad, para realizar todo tipo de trazado en piezas como por ejemplo ejes de simetría, centros para taladros, excesos de mecanizado
El Profundímetro es un aparato similar a un reloj, que como su nombre indica, marca la profundidad a la que se está.
Suelen llevar la esfera sobredimensionada para facilitar su lectura. Si el modelo es de agujas se recomienda que tenga un campo de lectura entre los 0 y los 12 metros lo más amplio posible, para facilitar el control de paradas.
Es un aparato frágil, que debe lavarse con agua dulce después de cada inmersión. Si las agujas no vuelven a la posición de 0 metros revíselo.
Tipos de profundímetros
• Profundímetro capilar: es el más barato, pero más inexacto solo aconsejable para profundidades inferiores a 10 metros. Funciona según la Ley de Boyle con una burbuja de aire que se desplaza por el interior de un tubo dependiendo de la presión ambiental. Casi no se fabrican.
• Tubo de Bourdon: el cual funciona según el principio de deformación de un tubo curvado en forma de espiral al que se le aplica una presión.
• Profundímetro de diafragma o membrana: tienen una cámara húmeda, donde el agua presiona sobre el diafragma que se deforma según al presión.
Estos dos últimos son más caros pero más exactos. Se debe saber que están calibrados a nivel del mar, y que si la inmersión es en un lago de montaña se deben hacer los cálculos adecuados para saber la profundidad.
Es aconsejable que lleve una segunda aguja, llamada de memoria, que sirve para marcar la máxima profundidad de la inmersión.
• Profundímetro electrónico: lee la presión a través de una pequeña carga. También da lecturas de él tiempo de inmersión, la profundidad máxima alcanzada, temperatura… Algunos incluyen alarmas sonoras que indican si se asciende a una velocidad superior a la prefijada. Su medida se basa en la presión absoluta real, no en la atmosférica como los otros, teniendo una precisión de 0,5 metros.
Goniómetro

Un goniómetro es un instrumento de medición con forma de semicírculo o círculo graduado en 180º o 360º, utilizado para medir o construir ángulos. Este instrumento permite medir ángulos entre dos objetos, tales como dos puntos de una costa, o un astro -tradicionalmente el Sol- y el horizonte. Con este instrumento, si el observador conoce la elevación del Sol y la hora del día, puede determinar con bastante precisión la latitud a la que se encuentra, mediante cálculos matemáticos sencillos de efectuar.
También se le puede llamar sextante. Este instrumento, que reemplazó al astrolabio por tener mayor precisión, ha sido durante varios siglos de gran importancia en la navegación marítima, hasta que en los últimos decenios del siglo XX se impusieron sistemas más modernos, sobre todo la determinación de la posición mediante satélites. El nombre sextante proviene de la escala del instrumento, que abarca un ángulo de 60 grados, o sea, un sexto de un círculo completo.
Existe un instrumento llamado goniofotómetro, fotogoniómetro o fotómetro de celda móvil, que mide la intensidad luminosa emitida por una fuente de luz (generalmente de tipo artificial) a diferentes ángulos, se utiliza para conocer la curva de distribución luminosa, la cual describe el comportamiento de la fuente de luz.
El goniómetro es un instrumento de medición que se utiliza para medir ángulos, comprobación de conos y puesta a punto de las máquinas-herramientas de los talleres de mecanizado.